Share this article:
Key Takeaways from this article
The Hidden Causes of Delays in Construction Projects
The screed layer raises his hands apologetically, shrugs his shoulders, and turns down the corners of his mouth. His material storage on the 3rd floor is exactly where the electrician was supposed to install the distribution box today. 'I didn't know that!' he says as he turns around.
Instead of laying screed, he and his colleague will spend the next few hours relocating their storage. Meanwhile, the electrician, who had come specifically for the distribution box, is sitting around. The project accumulates further delay.
As a construction or project manager, you are familiar with these situations. They are commonplace in construction site management in numerous variations: One trade doesn't know what the other is doing. They get in each other's way, hinder or even endanger one another.
And the scheduler shakes his head. He had considered all of this in his detailed schedule. 'But no one here takes it seriously anyway,' he says resignedly and goes back to his construction container."
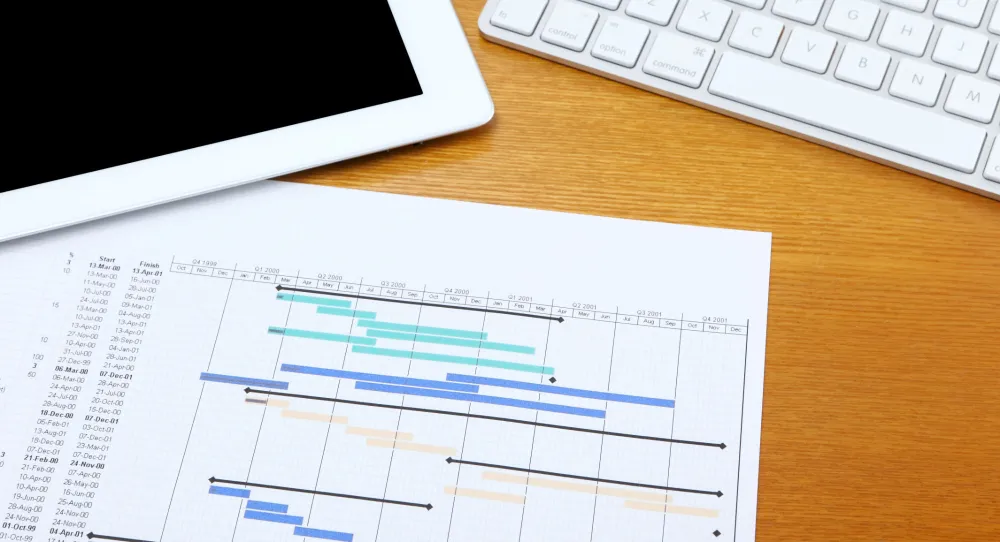
Why Gantt Charts Fall Short in Construction Project Scheduling
Why is coordination on construction sites often so difficult despite a sophisticated Gantt schedule?
Everyone is familiar with the classic Gantt chart used for scheduling. In a Gantt chart, tasks are listed vertically on the Y-axis, typically in chronological order of execution. The timeline, displayed on the horizontal X-axis, shows the duration of each task, with bars representing their start and end dates. Tasks are often linked with dependencies, showing how one task must be completed before the next can begin.
In theory, a Gantt chart’s visual layout simplifies the planning and monitoring of deadlines and is meant to promote communication within the team. In reality, however, a Gantt chart can quickly become overwhelming and difficult for most people to understand.
This is especially true for larger projects with many dependencies. Only the experts can often make sense of the chart, while others mentally check out when 15, 20, or more rows of bars start to blur into one another.
A quick glance at the participants during a construction meeting is usually enough to see who is still engaged and who has already mentally drifted off, likely preoccupied with one of the many problems on the construction site. Yet, despite this disconnect, when asked, most people still respond with “Yes, everything's clear, boss!” Just get out of here quickly. Finally, back to the real work—there’s plenty to do.
As a result, everyone returns to their individual tasks, focused only on their own problems—issues that really should have been resolved collaboratively during the meeting.
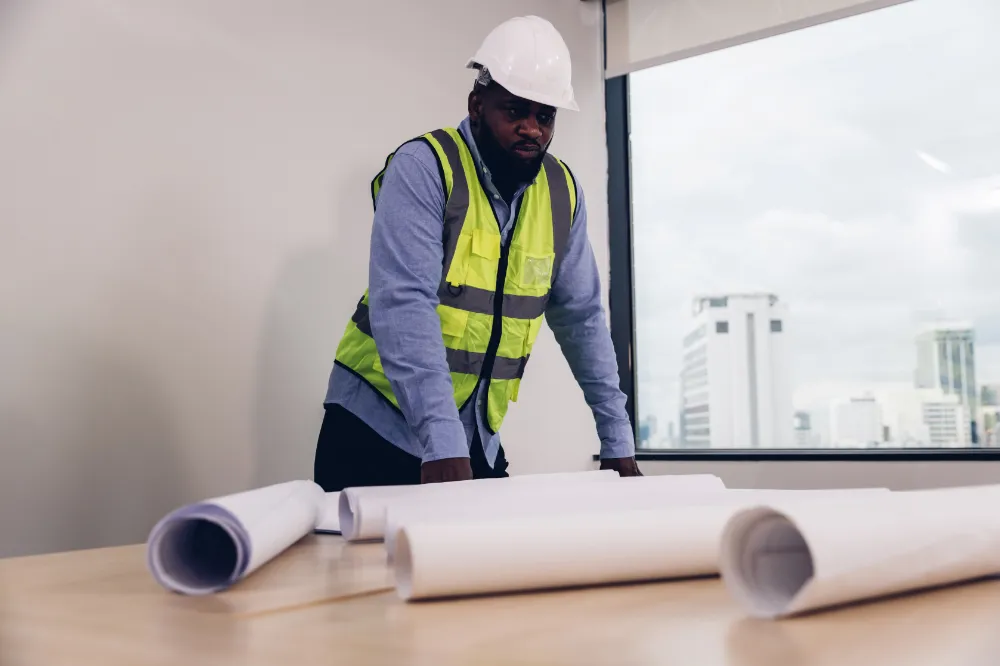
Zone Planning as a Solution to Gantt Chart Complexity in Construction
Unlike the Gantt chart, a process plan using zone planning is perceived by participants as intuitive and easy to understand. On the Y-axis, the project is divided into zones. These zones could represent specific parts of the structure (such as the main building, ground floor, or office 1) or individual project phases (e.g., design phases like LP 1, LP 2, LP 3, etc.). Additional levels of detail can be assigned to each zone as needed.
In this application, swimlane diagrams are used to enhance the clarity of zone planning by visually organizing the tasks—or “process steps”—into lanes. These lanes distribute tasks on the timeline in the order of execution, with individual color codes helping the participants to navigate the plan more effectively.
Integrating swimlane diagrams into zone planning provides a clear, structured approach to managing complex construction projects. This utilization of swimlane diagrams in zone planning exemplifies their broad applicability and effectiveness in organizing and clarifying process flows in construction management.
To explore how swimlane diagrams can further optimize your construction management process beyond traditional zone planning, see our comprehensive guide in the article, "Swimlane Diagram Mastery for Effective Process Mapping & Process Flow Optimization in Construction."
The benefits of this type of process plan are clear: It is simple to comprehend and provides all team members with a clear, organized overview. Even non-technical staff, such as those in purchasing or commercial support, can quickly understand what is needed, when, and where.
Task dependencies are easy to identify, and parallel activities happening simultaneously are clearly visible. Recently, a project manager working on a multipurpose hall explained how the process plan helped him precisely coordinate workflows.
For safety reasons, no work could be performed on the ground in areas where ceiling installations were happening. “If a heavy wrench falls from 20 meters, not even the best hard hat can help,” he explained. Thanks to the process plan, he could identify this safety risk and adjust the work sequence accordingly. The plan was easy for everyone involved to understand, helping the team internalize the project’s complexities.
“The same goes for our construction meetings,” the project manager added. “We’re all under intense pressure every day. Everyone needs to understand the situation within a couple of minutes. With the process plan, this is much easier. I don’t get blank stares anymore—everyone immediately knows what’s going on. We no longer hear ‘I didn’t know that.’
Lcmd: Bringing Simplicity and Real-Time Updates to Planning in Construction Project Management
Projects face countless challenges and dependencies every day. To maintain control, participants need to quickly and easily get an overview of the project's progress.
Lcmd software helps you to create a process plan in no time, even from existing Gantt charts. The plan can also be adjusted and updated in real-time based on the actual conditions on the construction site. In large projects, filters help you focus on the essentials. With Lcmd, you can keep even complex project workflows up to date, simple, and easy for all participants to understand.
{{cta}}